Electromechanical Resource Center
Tools and Information for Electric Motor End Users
Your electromechanical equipment keeps your systems working. With proper maintenance and care, you can obtain the longest, most efficient and cost-effective operation from general and definite purpose electric motors.
Getting the Most from Your Electric Motors
Get more information on the following steps to ensure a quality installation and reliable operation of a repaired or replaced motor.
Basic Motor System Considerations
Safety + Environment Considerations
Motor Data + Verification
Motor Foundation + Base
Electrical Connections
Alignment + Vibration
Startup Procedures
Motor/System Baselines
Methods for Determining Motor/System Baselines
Find out more about these application-specific considerations for operational monitoring and maintenance.
Basic Motor System Considerations
A motor system typically includes the power supply, mounting, coupling and driven equipment.
- Follow all applicable electrical codes.
- Lock out and tag out all potential energy sources before working on the motor.
- To avoid electrical faults, make sure connections are right and appropriately insulated. Don’t use wire nuts.
- Record the motor no-load current on the motor data sheet.
- Install the connection box cover.
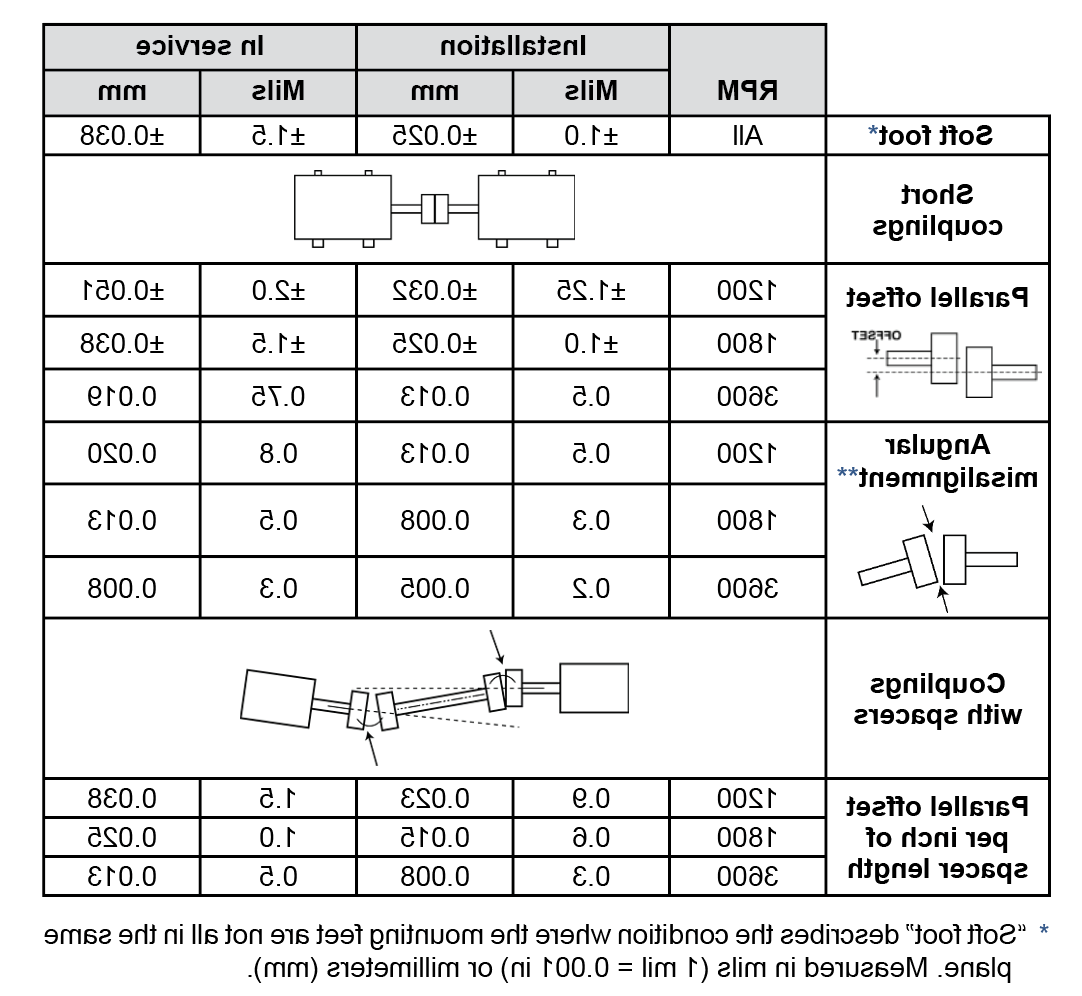
- Inspect and clean the motor to restore it to “as shipped” condition. If the motor has been subjected to vibration, disassemble it and check for bearing damage. Replace any damaged bearings. On grease-lubricated motors, the bearing cavities should have been filled with grease for storage.
- To protect the windings from contamination, remove the drain plugs before adding the lubricant specified on the lubrication plate. Then purge the old or excess grease from the bearing cavity by running the motor at no load for 10-20 minutes and replace the drain plugs. If any moisture is present in the purged grease, the bearings are probably rust damaged and should be replaced.
- If the motor has been stored for several years, the grease has likely dried out or separated, and the drainpipe is probably plugged up. In that case, it will be necessary to disassemble the motor, clean out the old grease and repack the bearings with the appropriate amount of the specified lubricant. To prevent winding contamination, drain oil-lubricated motors before moving them.
- After installation, fill the reservoir with the manufacturer’s recommended lubricant. Test the winding’s insulation resistance and dielectric absorption ratio and record the results. If the IR and DAR test results are satisfactory, perform no-load test operation.
- If the motor operates normally, allow it to reach full speed before shutting off the power. Always lock out and tag out the motor before connecting the driven load. Once the motor and driven load operate properly, record the full-load voltage and current for all three phases on the motor data sheet for this installation. If possible, also record the input power with load.
- If the motor is so equipped, monitor the bearing and winding temperatures until they reach a steady state. Document these values as well as the ambient temperature and humidity. For critical applications, record the initial vibration signature of the complete machine as a baseline for a predictive maintenance program.
To maximize equipment life, compare baseline installation data from your motor data sheet with future test results as part of a preventive or predictive maintenance program. Trending the data helps operators recognize changing conditions and prevent catastrophic failures. Should a failure occur, trending could also help identify the cause.
PRO TIP Local service center professionals can be invaluable resources for this. Find one near you.
- Load current, speed and terminal voltage. These changes usually indicate that a vital system component is damaged or about to fail. Other electrical tests may include insulation resistance, lead-to-lead resistance at a known temperature, no-load current, no-load voltage, and starting characteristics.
PRO TIP Some changes in the current and speed may be normal, depending on the type of load.
- Motor current signature analysis. This test diagnoses squirrel cage rotor problems. It’s more accurate if a baseline is established early in the motor’s life.
- Mechanical tests. These normally consist of measuring shaft runout and checking for a soft foot.
- Vibration. Although overall vibration readings can be used as baseline data, Fast Fourier Transform spectra in all three planes at each bearing housing are preferred.
- Infrared thermography. This tool can detect changes in the operating temperature of critical motor components, especially bearings.
- New motor baselines. Comparing factory terminal winding resistance and no-load amps with data taken under load can be useful when monitoring the condition of a new motor or troubleshooting system problems. Factory baselines are often available from the manufacturer or its website. The accuracy of factory data depends on how it was obtained, but it’s usually sufficient for field use.
Baseline data for a newly installed motor could reveal an error and prevent a premature motor failure. Rather than simply “bumping” a motor for rotation before coupling it to the load, operate it long enough to measure the line current for all three phases, as well as the voltage and vibration levels.
PRO TIP Comparing the baselines of a failed motor and its replacement could reveal application- or process-related weaknesses in the system.
Repaired motor baselines. Service centers usually provide no-load and/or full-load test data for repaired motors, including voltage, current and vibration spectra. Comparing these results with historical baselines and those obtained onsite when the motor is returned to service may confirm the quality of the repair or possibly reveal underlying system problems. For newly repaired motors that have been in operation many years, baseline comparisons are invaluable for root cause failure analysis and may even expose consequential damage from certain kinds of failures. To correctly identify cause and effect and prevent a recurrence, always investigate equipment failure at the system level.
Power factor is the ratio of kW (kilowatts) to kVA (kilovolt-amperes) in an AC circuit, which for a given load (kW) will be between 0 and 1.
Raising a low power factor will decrease the current flow through the motor’s power cables and other equipment and therefore reduce heating and thermal aging. It may also reduce energy costs (where applicable) by decreasing or eliminating electrical utility surcharges for low power factor.
This figure shows where power factor correction capacitors could be installed in a motor circuit. Location 2 is usually best for most motors, and Location 3 is usually better than Location 1.
- Locations 2 or 3 are offline when the motor is offline; Location 1 is always energized. This could lead to overvoltages and transient torques if other motors or other inductive equipment are on the bus.
- Location 3 requires downsizing the protective devices because of the reduced current flow.
- Location 3 could introduce high amplitude switching transients or current surges into motors that jog or switch frequently–e.g., elevator, multispeed, open transition autotransformer or wye-delta start motors, and some part-winding start motors (except so-called extended- or double-delta models). Location 1 is better for such applications.
PRO TIP Use power quality monitoring equipment to detect haronics and filters to control them, extending your motor's life.
Getting The Most From Your Electric Motors
This 40-page booklet provides great advice for obtaining the longest, most efficient and cost-effective operation from general and definite purpose electric motors.
This booklet covers topics such as:
- Installation, startup and baseline information
- Operational monitoring and maintenance
- Motor and baseline installation data
- How to read a motor nameplate
- Motor storage recommendations
LEARN MORE AND DOWNLOAD MÁS INFORMACIÓN Y DESCARGAR BUY PRINTED COPIES
EASA-Authored Articles from Industry Publications
The Big Four Factors Affecting Motor Health
Balancing plant maintenance costs and activities with the need to achieve production goals is a daily challenge for most maintenance professionals. Since the motor-driven system is often a critical component in this dynamic, this article looks at some best practices to help it achieve those goals and meet customer demands.
New ANSI/ASA Shaft Alignment Standard Adopted
The procedure for aligning two rotating machines requires measuring their relative shaft positions and adjusting one or both machines. Until recently, though, how closely the shafts need to be aligned was an open question. That changed with the publication of American National Standards Institute/Acoustical Society of America (ANSI/ASA) standard 2.75-17.
The Shape of What’s Shaking
This webcast will focus on identifying resonance and then move to methods that help visualize the vibratory motion, helping to identify solutions.
Evaluate Noise in Electric Motors
Determining the source of noise in a motor is often much more challenging than correcting it. However, a methodical approach to investigating noise can narrow down the possible causes and therefore make resolution easier.
A Simple Approach to Duty Ratings of AC Machines
Before putting an AC machine into service, make sure its duty rating matches the application requirements. Otherwise, there’s a good chance excessive heat will degrade the machine’s windings.
Reject These Motor Myths
The tongue-in-cheek saying “If it’s in black and white, it must be right” is a helpful reminder that not everything we read (or hear) is accurate or complete. It’s always best to check sources and verify facts before accepting consequential statements as true. This article provides a selection of common misconceptions about three-phase squirrel-cage motors and the facts that deny them.
Sizing Pumps and Pump Motors
End users or service centers often need to specify replacement pumps or pump motors, sometimes involving a retrofit or re-application project. A successful outcome depends on accurate assessment of application requirements and a good understanding of the parameters that govern pump performance.
Bust Nine Common Motor Myths
Here’s a random collection of common misconceptions about three-phase squirrel-cage motors and the facts that deny them.
Electric Motor Noise: How to Identify the Cause and Implement a Solution
Determining the source of noise in an electric motor is often more challenging than correcting it. A methodical investigative approach, however, can narrow the possibilities and make it easier to resolve the issue—with one caveat. If the noise is due to something in the motor design (e.g., a manufacturing defect or anomaly), a solution may be impossible or impractical.
Best Practices for Electric Motor Storage
Storing an electric motor for more than a few weeks involves several steps to ensure it will operate properly when needed. Factors like temperature, humidity and ambient vibration in the storage area also influence the choice of storage methods, some of which may be impractical for smaller machines or need to be reversed before the motor goes into storage.
Advice: Effects of High or Low Voltage on Motor Performance
To ensure the reliability of an RV’s electrical devices, especially electric motors, campers must know the service voltage of the hookup their RV is using. Teaching consumers to check that before they plug in the vehicle could save them many headaches.
Making Shaft Lift Adjustments in Vertical Turbine Pumps
Vertical turbine pumps (VTP) commonly have rotors with multiple mixed-flow impellers (sometimes 12 or more) that are supported by a vertical pump motor. Such designs offer a lift adjustment for raising or lowering the pump rotor to properly position the impellers within the bowl. Depending on the type of pump, this may be critical for maximizing pump efficiency and could have a significant impact on motor load (current) and reliability.
How Up-Thrust Occurs in Vertical Turbine Pumps and Provisions to Control It
Vertical turbine pumps depend on the vertical motor's thrust bearings to support the combined weight of the pump rotor and the motor rotor and to counteract the dynamic down-thrust that the pump impellers generate in lifting the liquid.
Why permanent magnet motors and reluctance motors are finding increased industry application
Those familiar with industrial electric motors have heard “DC is dead” for decades as advances in variable-frequency drive (VFD) technology for AC squirrel cage induction motors (SCIMs) seemed destined to replace their DC counterparts in every conceivable application.
But just as DC’s demise was greatly exaggerated, so too is the prospect of successor technologies replacing the installed base of SCIMs any time soon – whether for new applications or replacement motors.
Increasing Motor Reliability
Regardless of the method used to detect winding temperature, the total, or hot spot, temperature is the real limit; and the lower it is, the better. Don’t let excessive heat kill your motors before their time.
Converting motors from horizontal mount to vertical mount
Occasionally an end user wants to take a motor designed for horizontal mounting and use it in a vertical position. This article addresses some of the key mechanical factors that should be considered when applying a horizontal ball-bearing motor in a vertical mounting position.
How to deal with wet or flooded motors
Flooding in the aftermath of tropical storms, including hurricanes, monsoons and cyclones, and with their associated heavy rainfall can shut down hundreds of plants along the Gulf Coast, from Florida to Texas, as well as in other places around the world. And they are doing so more often. To get them up and running again, maintenance departments and motor repairers face the daunting task of cleaning muck and moisture from many thousands of electric motors and generators. The process involved in such situations can take weeks, if not months, and requires special clean-up procedures for motors contaminated by saltwater.
Wear ring clearance for centrifugal pumps
One of the most common repairs on centrifugal pumps is replacing worn or damaged wear rings. To restore efficient, reliable operation and prevent catastrophic pump failure, it is critical to restore proper clearances between the stationary casing wear ring and the rotating impeller wear ring. Although many pump manufacturers provide clearances and dimensions, some do not. There are plenty of aging pumps around from now-defunct manufacturers for which dimension data is simply not available.
In such cases, the rule of thumb that follows provides some guidance for acceptable running clearances, or the minimum running clearance chart in American Petroleum Institute (API) Standard 610 can be used as a guide.
Considerations for using VFDs with standard motors
End users desiring speed and/or torque control often buy variable-frequency drives (VFDs) to modify existing applications where a standard induction motor is in place. Frequently, they try to control costs by using that existing standard induction motor. Before taking that path, however, it is best to consider a few areas of concern with the approach.
Selecting Replacement 3-Phase Squirrel Cage Motors
Selection of replacement motors is usually straightforward if the ratings are equivalent. Sometimes, however, a different type of motor is necessary or desirable. For success in these cases, it is essential that the replacement motor provide the required performance — and do so reliably.
Know your degree-of-protection codes
The International Electrotechnical Commission (IEC) standard 60529, “Degrees of protection provided by enclosures (IP code),” addresses the degrees of protection for electrical machines (motors and generators). The “IP” acronym means “international protection” but is sometimes referred to as “ingress protection.” The IP code is commonly displayed on the nameplates of metric machines that are manufactured to IEC standards.
EASA explains upcoming pump standards
Starting in January 2020, the U.S. Department of Energy (DOE) will begin implementing the first ever energy efficiency standards for freshwater rotodynamic (centrifugal and axial flow) pumps. These standards will directly affect pump manufacturers and, to a lesser extent, the pump repair market, while ultimately benefiting end users if the new focus can reduce their energy costs.
What’s in a nameplate?
Whether you're selecting a motor for a new application or a replacement for one that has failed, you need a reliable way to match the capabilities and performance characteristics of various motors with the requirements of the application.
Motor maintenance trends: 6 factors to evaluate
When faced with an ailing or failed motor, plant operators typically consider whether to repair or replace it. According to a 2014 study conducted by Plant Engineering magazine for the Electrical Apparatus and Service Association (EASA), just more than one-half of plants have a policy of automatically replacing failed electric motors below a certain horsepower rating. While that horsepower rating varied depending upon the plant’s installed motor population, the average rating was 30 hp.
While such policies address a portion of the motors used at most plants, they do not cover what occurs with those motors. That question was addressed in a more recent research project commissioned by EASA that focused on the disposition of electric motors considered for repair.
Best practices for vertical turbine pump repair
Vertical turbine pumps (VTPs) are workhorses in the petrochemical, power generation and manufacturing industries, and prolific in municipal water applications that handle the primary intake load. Although these machines are ruggedly built, abrasive sediments in the pumpage take a toll, particularly on line shaft and pump bowl bearings, so periodic overhauls are often necessary. Rather than simply replacing the bearings, however, it is important that repairs address all of the issues needed to restore maximum operating life.